【轻量化高峰论坛】长春捷翼冯思铭:新能源与传统汽车线束系统轻量化与低成本化的挑战与解决方案
7月12日-13日,“2018中国汽车轻量化产业高峰论坛”在上海隆重举行,论坛以“新技术、新材料、新工艺“为主题,旨在降低汽车自身重量同时提高输出功率、降低噪声、提升操控性和安全性,并对汽车轻量化政策趋势发展、整车轻量化平台化设计方案、关键零部件轻量化技术开发及汽车轻量化多材料应用及成本控制分析等问题展开探讨。
长春捷翼汽车零部件有限公司产品设计部经理冯思铭
长春捷翼汽车零部件有限公司产品设计部经理冯思铭分别就新能源与传统汽车线束系统轻量化与低成本化的挑战与解决方案展开分析,以下是演讲实录(有部分删减):
长春捷翼主要的市场是以铝线束为主,目前无论是在国内还是国外,主要都是用一些压接,或者其他的方式完成铝线束的转换,但铝线束本身的延展性很差,无论在压接还是机械性能方面,不会达到非常好的效果。因为之前各位领导已经讲了在整车这一块,轻量化减重所占的比例,线束可能不起眼,但是整车都离不开线束,线束就如同车辆的血管一样。据我们分析,整车线束,包括动力电池里面的线束等等,由于电压增强,线束的载流量会增大,带来的是线束的直径、长度的增加。目前 80%以上的汽车线束都是铜做的,因为铜无论从延展性包括载流量都是很好的,国内目前大多数的优质铜都是进口的,铜的价格比每个月的浮动非常大,包括现在每一吨在 5-6 万之间的比例。
我们跟美国的贸易战争价格将被控制的很严重,它将直接影响我们的整车线束,因为线束用的铜很多,不光是蓄电池线束,还有门板线束等方面成本都会增加。随着这种成本的增长,我们更多的是将目光集中在铝线束这一块,无论是新能源、轻量化、还是成本降低,都是我们现在更专注的事业。相应的一些标准,例如德国的 LV 112,甚至国标都推出了一些关于铝线这方面的信息。
就像我刚刚说到的,我们现在可能 80%-90%以上的汽车用的是传统线束,而铝线束现在用的都是一些传统的压接铝线束,铝代替铜,有什么不好的方面呢?因为铝的延展性很差,无论在压接过程中还是做实验或者是实车路试的过程中,无论是振动还是环境的影响都会对压接的部分产生不良影响,会有电化学反应,接触不良,烧车。大众、奥迪现在有很多车都是蓄电池后置,导致很多线束都是很长,甚至 6-7 米以上,MPV 的车型更长,大概 8 米左右。我们现在跟宇通客车在合作,大概需要 120 平方的铜线,我们转换成 240 平方的铝线之后,去现场装车拿着 8 米长 120 平方的铜线两个人装都很吃力,用 240 平方的铝线装车,工作人员需要一个手拿着到现场就可以,线径越大,越长,成本降低的越明显,重量减轻的效果也就越好。
我们也是从 2014 年开始对外,因为从 2009-2014 年,我们在给一汽大众做原始的配套项目,我们做的铝线束都是焊接完成的,包括摩擦焊接,等离子焊接。这两种方式之前由于外国主机厂的专利和设计保护,是不允许给我们国内的一些主机厂进行供货的,甚至包括技术推广。但后来我们得到了技术授权和突破,从 2014 年到 2016 年,随着国产化的加剧,我们开始给国内的一些主机厂做铝线束的推广和技术支持,我们 2016 年走进了吉利、比亚迪、宇通、捷豹路虎等等。之前吉利的产品总长有 5-6 米,他们当时用的技术是压接,这个技术在吉利内部受到了很大的争议,沃尔沃公司那边不同意用压接方式处理,他们在进行试装的过程中,经过电流的加载,两边做一个铜板进行阻挡,再经过加载电流很长一段时间之后,铝线束在压接的部分直接烧掉了,附带着火花把两侧的铜板给烧了。铝线束无论是从布局还是焊接工艺,随着它的截面积增大,会出现很多问题。但许多客户对铝线的性能不是太熟悉,所以我们不单单是把焊接这项技术带过来了,我们是把整个技术团队带到各个主机厂,我们会从客户的白车身一直到整个所有的配件,整个过程我们把所有这根线束布局做一个优化,做一个完整的方案的设计,包括 48V 电机,包括电池,甚至包括动力电池所安装的位置,以及周边环境给大家设计铝线束,包括弯曲半径多大,需要有多大配合间隙,材料的使用等等。
这是世界上对铝线束技术发展的趋势,现在比较成熟的,在德国大众比较认可的,是摩擦焊的技术,包等离子焊的技术,它在机械性能和焊接性能都非常优秀,可能有些人知道有超声波焊接,虽然超声波焊接本身的拉拔力是没有问题的,但是撕拉力容易存在问题,且设备投资巨大,加工成本过高。另外,超声波焊接是不允许进机舱的,所以我们现在主推的是摩擦焊接和等离子焊接。现在像电磁焊接等等是我们针对于铝线束开发的新技术。
大家看到的是我们现在当下无论是德标、美标、国标我们现在用的铝线束的大概配比,这边大家可以看到,相对原始的铜线束,蓄电池铜线束 35 平方的,可以用 59 的铝线束代替。吉利集团我们已经覆盖了 95%以上所有平台的铝线束供应,48V 的电池用的 70 的铝线束。现在我们公司所研发的主推项目,是向各个主机厂推动铝线束产品的实际应用,包括带屏蔽网、不带屏蔽网的高压铝线束,还有低压铝线束,不局限于圆线,还可能是扁线,在奥迪、吉利我们大力推广的,扁线折弯的性能很好,我们可以通过全自动化的折弯机按照我们给客户的原始设计方案进行处理,可以根据底盘整体的造型实现全自动化的折弯,整个底盘造型力求把扁线弯折出来,白车身可以直接把这个扁线放进去。而原始的铝线束,很多主机厂都是挂在车身外边加了很多护板,我们这跟扁线束非常矮,可以直接放在底盘内部,放在跟地板部之间的位置,无论从本身的布局上,还是节省护板的开销上,都有很大的好处。这种好处的本身,是由这种扁线都是通过弯折折出来的,每个折弯角度定型效果很好,所以可以直接扣在底盘每个转角的位置,在定位件上也有很大的节余。考虑各方面的成本,会节省很多费用,因为不需要任何护板,且是放在车身内的,有效保证了线缆的安全性。另外,现在圆线需要 4-5 个塑料的护壳保护它做定位,这种扁线直接就卡在底盘上就可以了。
目前我们针对于这种圆线也好,扁线也罢,大致的运用的点是在哪?第一像 48V 电池跟 BS 电机相连接的正负线,我们现在的焊接方法除了原来压接的方式,本身这种性能上包括机械性能,包括化学腐蚀性能等都很好,且可与空气进行隔绝。另外一方面我们现在产品给很多做 PACK 的主机厂在做,PACK 里面有很多高压的铜线,我们自己生产的这种高压的铝线包括有屏蔽的,无屏蔽的,包括扁平的,现在 PACK 里面有大量的应用,我们跟做 PACK的主机厂深度的合作。成本的降低和重量的降低对 PACK 的成本和重量也会有明显效果。
这张图是我们捷翼的流程,因为 CEO 没有来,简单提及一下,我们 CEO 是从美国回来的,他很年轻,他带回来的想法是我们作为一家民营企业,我们必须立足于研发,作为企业的发展根本,而研发主要针对线束这一块,必须要做好做强。至今,研发人员 200 多人,通过 5 年的时间做到了这样的研发流程,涵盖 TRIZ、DOE、DFMA 等等,我们在加工的过程中很多都是用 DOE 的分析方式来确保最重要的参数在一个水平上。焊接的方式不像压接,压接可以做切片可以做破坏性的实验确保压接的过程是否稳定,焊接无法在线做到百分之百每个剖切出来,我们更多的是把这一部分的安全隐患包括这一部分的研发放在前期,我们用DOE 分析上千个案例,保证每一个焊接的端子跟焊接的线束都是非常良好的状态,能达到我们要的所有的参数都是非常稳定的,且上下不会有很大浮动的状态。
铝线本身折弯也好延展性也好,包括抗振动的强度没有铜线那么好,我们跟客户做深度研发的过程中,尤其在前舱,前舱空间非常小,加上周边的环境数据非常复杂,我们会给一个最优化的设计方案。这一张图是我们在实车上给客户的安装对比,这是我们给大巴车的主机厂做的试装。现在上面那幅图是原来 120 平方铜线大概 8 米长安装的方式,下面是 240平的铝线的安装。虽然曲率和折弯半径比铜线要小,我们可以通过绝缘皮不同的选择,比如说硅胶或者更好原材料的配比,包括导线,绞合的方式,可以控制尽可能达到铜线折弯半径。第二个可以看到 240 平方的铝线可以在很小的空间内进行很大的弯折。
敬请关注盖世汽车“2018中国汽车轻量化产业高峰论坛”直播专题:
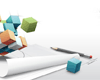
温馨提示:出口供应商服务是盖世汽车网根据汽配行业特点,依托盖世B2B业务,利用盖世丰富的买家资源为中国汽配出口企业精心打造的贸易平台,旨在帮助中国汽配出口供应商积极对接国际售后市场,扩大汽配产品出口,拓展海外业务。
若您还有出口贸易方面的困惑,点此联系我们